Spark plugs, those parts responsible for engine combustion, could soon be replaced by laser ignition systems. They will take the place of spark as a mean of primary combustion of air-fuel mixture in the engine, resulting in increased energy efficiency and reduce carbon emissions.
In a conventional engine with internal combustion , fuel-air mixture is compressed by a piston and ignited by a spark plug splaced on top of the cylinder. This spark is generated by electric arc created between two electrodes, a method good enough to ignite the fuel, but also limits the range and types of fuels that can be burned.
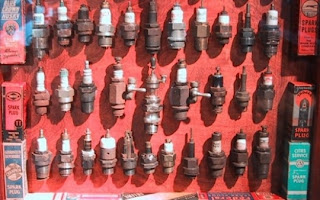
An engine (almost) ideally work with a small amount of fuel and would provide a stronger spark. Is fixed what can provide laser combustion systems, created by a joint team made up of romanians and japanese.
Laser ignition can be adjusted so as to have greater precision than spark plugs, increasing combustion efficiency and improving engine economy. Furthermore, lasers can be channeled to ensure ignition anywhere in the cylinder (spark plugs generate on the top, in the opposite end of the piston).
Lighting by laser can focus on core of compressed fuel-air mixture, allowing controlled explosion spread evenly over each cylinder, where a higher power for each engine times. Laser can ignite fuel even in two places simultaneously, creating a more effective explosion , a more complete burn of the liquid in the tank.
Power lasers in the past with all these processes should exist, but their implementation was unfeasible in auto engines, were bulky, heavy and unstable. Now, new high-power lasers, made of ceramic powders have diameters of only 9 millimeters each.
These ceramic devices accumulate the energy of compact lasers, of lower power whose rays are transmitted through optical fiber and released in pulses with durations of only 800 trillionth of a second.
Unlike the delicate crystals normally used for high power lasers, ceramic is more robust and can better manage the heat generated in internal combustion engines. The team of inventors is already in discussions with Denso, a major automotive component manufacturer, to market the new technology.
Until hydrogen engines become commonplace in cars, laser ignition can sooner be implemented to reduce fuel consumption and carbon emissions in a car.
by "environment clean generations"
0 comentarii:
Post a Comment